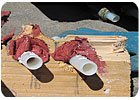
Contractors need to make sure the products they are using are tested and are compatible. The firestop (red putty) PEX tubes used here-and in 75 condominiums-had a chemical reaction that caused pinhole leaks, and had to be replaced at significant cost.
A Firestop System is defined as a passive fire protection system comprised of a variety of components used to seal openings through fire-rated wall or floor systems. Sometimes these are referred to as “poke through” openings. The openings may be electrical wiring, mechanical penetrations, structural framing members, or a joint or junctions between rated wall or ceiling assemblies. Construction joints may be static or dynamic. Dynamic joints are more complicated, as they must remain in place to provide protection during a fire, after the joint has been subjected to the anticipated movement it expected to encounter during its service life. All firestop systems are routinely inspected, therefore we must all pay attention to design and installation.
Why such a big deal?
Some wall and ceiling contractors have noticed and commented that inspectors are getting pretty fussy about firestop systems. If you are wondering why such a commotion over something that will probably not happen and was not a big deal a few years ago, then we need to look back. Firestop systems got their birth in the 1970s with a few notable high-rise building fires that demonstrated the ability of fire to breach a properly installed fire-rated assembly. Fire disasters, like the MGM Grand in Las Vegas, led to more accurate records on fires and improved fire safety. Consider these facts from the National Fire Protection Association (NFPA).• Three-fourths of all fire deaths are caused by smoke inhalation.
• 57 percent of all people killed in fires are not in the room of the fire origin.
• 47 percent of survivors caught in a fire could not see more than 12 feet.
• Smoke travels 120-420 feet per minute under fire conditions.
Comprehending these undeniable facts gives us some appreciation for what building inspectors are up against. It also should make wall and ceiling industry contractors understand the importance of what we are charged with when we construct fire-rated assemblies: Protecting Lives.
The importance of firestops is certainly not lost on the building codes. The International Building Code (IBC) has two sections dedicated solely to firestops. The first is Section 712, PENETRATIONS. Section 712 governs the materials and methods used to protect through penetrations and membrane penetrations of horizontal (floor/ceiling) assemblies and fire-rated wall assemblies. The second is Section 713 FIRE-RESISTANT JOINT SYSTEMS. This section governs the joints installed in or between fire-resistance-rated walls, floors or floor/ceiling assemblies.

The insulating foam around this gas line penetrating a fire-rated ceiling does not meet firestop requirements
Proper Procedures
The architect is responsible for design and must decide on the methods of fire detection and protection required for the building occupants. This would include the compartmentalization, egress and the type of firewalls or smoke barriers required to meet the intent of the code for life safety requirements. Contractors are required to know how to construct and install these systems. Contractors could be held liable for installing a fire-rated system improperly. Contractors would also be expected to note obvious mistakes and/or deficiencies in systems designed by architects. Contractors have been found liable for missing or failing to notify the architect of what was considered an “obvious” disregard for life/safety or improper design. This is why it is important that contractors understand some “basic” rules about design and life/safety issues.Typically the architect should be specifying the appropriate firestop assembly for each penetrating item. The architect may employ an Engineer familiar with fire safety to review and provide consultation prior to submitting the plans to the building department. The architect/engineer needs to be aware of the type of penetration, the fire-rated assembly he/she has specified and the tested and approved firestop system that is appropriate. The tested assembly will have specified materials and limits to the size of the penetrating item. The tested firestop system will also be for a specified wall/ceiling assembly and cannot arbitrarily be used for other fire-rated assemblies. The tested firestop systems are done by qualified third-party code-approved testing agencies like the UL (Underwriters Laboratory), Intertek Testing Services (Warnock Hersey) or Factory Mutual (FM). All Firestop systems are required to be tested using the same test procedures. Testing is in accordance with procedures established in ASTM E 814 (UL 1479) for through penetration systems or ASTM 1966 (UL2079) for construction joint systems. These tests are to ensure that each designed firestop system will maintain the fire-rated integrity of the particular type of assembly in which it is intended for use. The systems are then assigned an F and T rating.
F Rating (Flame): An F rating is determined by the observation of flame through openings or on any element on the unexposed side of the firestop. A firestop shall be considered as meeting the requirements for an F rating when it remains in the opening for the duration of the fire and hose stream test.
Through penetration firestop systems for walls are required to have an F rating of not less than the wall penetrated (section 712.3.1.2)
T Rating (Temperature): A T rating measures the passage of flame and a rise in temperature of 325 degrees above ambient on the unexposed side of the firestop or penetrating item. A firestop shall be considered as meeting the requirements for a T rating when it remains in the opening for the duration of the fire and hose stream test.
Through penetration firestop systems for horizontal (floor/ceiling) assemblies are required to have an F and T rating of not less than one-hour but not less than the required rating of the floor penetrated.
L Rating (Leakage): An L rating is an optional test for air leakage through the firestop system. L ratings are typically reserved for smoke barriers.
Because it is impossible to test for every type of condition that a designer and/or contractor will encounter in the construction of a building, there is an allowable procedure known as “Engineering Judgments” for handling these unforeseen circumstances that still require firestopping. As the name implies, a judgment can be made to determine if a tested firestop system is appropriate for any unusual occurrences encountered that still require a firestop system. The Engineering Judgment must be developed in accord with sound engineering practices to ensure life safety and structural integrities concerns are not compromised. There are some basic rules on Engineering Judgments (EJ) that must be followed:
1. EJ shall not be used when a tested assembly is available.
2. EJ is to only be done by a qualified fire engineer.
3. EJ is only to the specific conditions for which that EJ was issued.
4. EJ is only for a specific job; transfer to another project site is not allowed.
5. EJ can only be used in jurisdictions that permit “Alternate Methods.”
Materials
There are many types of firestop materials and there is a good reason for this. The various materials are designed for the many types of penetrations and different penetrating items. For example a steel pipe and a plastic pipe may seem to be the same type of penetration, but the plastic pipe would melt in the event of a fire. This could potentially leave a large hole for fire, toxic gases and smoke to race through and thus breach the fire-rated penetration. One must also consider the components of fire-rated assembly. For example, concrete walls are very different than framed walls with gypsum wallboard. These would also be examples of where a contractor could still be found liable for using the wrong materials even if the architect specified the incorrect system or inappropriate use of that system. The firestop installer is expected to have some expertise and basic knowledge of the systems. So let’s cover the basics:INTUMESCENTS: Plastic pipe penetrating a fire-rated assembly is typically firestopped with an intumescent material. An intumescent swells or expands when exposed to direct flame or high heat (300 degrees F, 150 degrees C). Intumescents come in several forms, such as caulks, pipe collars, wrap strips and pads.
A word of caution: New products are coming on the market all the time. For example, Cross Linked Polyethylene (PEX) pipe is a new plastic product used for domestic water supply and is becoming very popular across the United States. The PEX is also used in hydronic heat systems. There are reported cases of some PEX brands being incompatible with some firestop F products. A chemical reaction occurred causing the PEX to prematurely age and develop water leaks.
As with any new products introduced to the market, firestop installers are advised to check the compatibility of materials with each manufacturer (PEX and the firestop manufacturer) before proceeding. Get it in writing from the manufacturer that the products are approved and compatible prior to proceeding.
PIPE COLLARS: A one-piece device containing intumescent strips within a metal collar that is made to clamp around a plastic pipe to direct the expansion of the intumescent. The IBC refers to the collars as “sleeves.”
MORTAR and GROUTS: Mortar or grout compounds are made from a variety of materials (usually cementitious), most are a non-shrinking setting type compound that keys to surrounding materials. Grouts and mortars are more popular on metal penetrations. These products do not expand in high heat.
SAFING: Usually a mineral wool product that is used to fill the annular space prior to the firestop material being applied. Safing should have the capability of withstanding temperatures of 1,832 degrees F (1,000 degrees C).
PUTTY PADS: A rectangular or square pad that is used to seal an electrical box in fire-rated assemblies. The material may or may not be made of an intumescent.
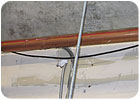
An electrical conduit is a “through” penetration of the rated gypsum wallboard and requires an approved firestop system.
Report Abusive Comment