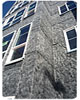
Section R703.2 of the 2006 International Residential Code requires that, “One layer of No. 15 asphalt felt, free from holes and breaks, complying with ASTM D 226 for Type I felt or other approved water resistive barrier shall be applied over studs or sheathing of all exterior walls. Such felt or material shall be applied horizontally, with the upper layer lapped over the lower layer not less than two inches (51 millimeters).” (The phrase “other approved weather-resistant material” encompasses asphalt-saturated building papers and polyolefin¹ housewraps, as approved by the local building official.²)
Many building professionals have only a hazy understanding, at best, of what brands of weather-resistant barrier membranes are (or are not) compliant with Section R703.2, other than the one prescriptive material identified in the code. For example, the typical inexpensive No. 15 roofing felt sold at many lumberyards is not manufactured with a sufficient amount of asphalt to achieve the IRC’s minimum weight requirements. The earlier version of the code³ called for a minimum mass weight of 14 pounds per hundred square feet. Some of the cheaper No. 15 roofing felts may have a total mass weight of as little as 8 pounds per square. Current requirements are a minimum felt weight of 11.5 pounds per square, a full 2.5 pounds per square less than in the earlier version of the code. The lesser the amount of asphalt used in roofing felt or building paper, the lesser the product’s ability to withstand rainwater saturation.
Further, many brands of roofing felts are manufactured only to meet the roofing performance requirements of ASTM D 4859⁴, not the stricter waterproofing performance standards imposed by ASTM D 226⁵, as required in Section R703.2. Typically, this information is provided by the manufacturer on the wrapper of the roll of felt. An asphalt-saturated felt that does not meet ASTM D 226 Type I specifications should not be installed behind a siding or cladding system. The use of a lesser quality asphalt felt can leave the builder liable if the product suffers a performance failure that leads to moisture or mold damage claims.
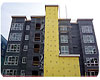
It is the responsibility of both the architect and the builder to use a building paper or wrap that is compliant with IRC Section R703.2.
Alternately, a builder can use one of the asphaltic building papers or polyolefin wraps that have been tested and accepted by the ICC Evaluation Service to provide a level of weather-resistive performance that meets or exceeds the performance of good quality asphalt-saturated felts. All such approved alternate weather-resistant barrier products have been issued an evaluation report that can be downloaded without charge from the ICC-ES Web site atwww.icces.org. The materials are tested much more than the requirements of Section 702.3 of the Code. ICC Acceptance Criteria AC 38 establishes the minimum physical property test criteria for weather-resistive barriers.
It is the shared responsibility of both the architect and the builder to confirm that a proposed building paper or wrap is compliant with Section R703.2, as demonstrated by issuance of an ICC-ES evaluation report or by an independent report of comparable testing acceptable to the local building official. Unsupported marketing claims about the performance qualities of a particular weather-resistant barrier product that has not been listed by the ICC-ES should not be accepted by the architect, homebuilder or local building official.
Note that the requirements of IRC Section R703.2 do not specifically address the complex issue of water vapor permeance (aka breathability) of the approved asphalt-saturated felt, building paper or polyolefin housewrap. However, these additional physical properties are addressed for products accepted under AC 38.
In many regions of North America, the primary orientation of the vapor drive through exterior walls during winter months is outward from the warm, humid interior spaces. The building code mandates that residences be designed and constructed to accommodate both exterior and interior humidity loads in such a manner that excess moisture accumulation does not occur within the building interiors or the exterior walls. The IRC does grant, however, broad leeway to the project designer to determine how best to resolve moisture loads expected in a specific building envelope design at a specific locale.
Depending on many variables, including exterior and interior humidity and temperature conditions, the presence (or lack) of mechanical ventilation and/or air-conditioning at the building interior, the presence (or lack) of an interior vapor barrier and the overall permeability of the exterior wall assembly, the breathability of the water-resistant barrier membrane can be a critical factor in determining whether or not moisture condensation and mold growth may occur.
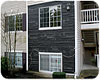
Installed Jumbo Tex 60 Minute Building Paper
WHAT'S IN A PERM?
The unit of measurement for water vapor permeance is the perm.6 Some building envelope designs (and their designers) favor a water-resistant barrier with a relatively low perm rating (an approved asphalt-saturated felt, for example, has a breathability of about 5 perms). Other designers may call for the moderate vapor permeance (10-20 perms) offered by Grade D building paper and many of the polyolefin wraps or perhaps the high vapor breathability (50+ perms) afforded by some polyolefin wraps. One major spun-bonded polypropylene wrap boasts an astounding breathability of 212 perms.All of these water-resistant barrier membranes have been tested and approved by ICC-ES; however, designers and builders should not misconstrue these listings to mean these various products will provide equivalent, interchangeable performance. For example, consider the simple, but critical, differences between Grade B and Grade D building paper. The breathability of a good quality Grade D building paper exceeds 10 perms, while the permeance of a good quality Grade B building paper by the same manufacturer is less than 1 perm. In other words, as reported by its manufacturer, the breathability of the Grade B paper is so low that the product constitutes a traditional vapor barrier.
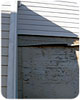
Vapor condensation has occurred at the gypsum sheathing behind the Grade B building paper. (Photo Credit: Lonnie Haughton)
The potential effect of installing a vapor barrier under lap siding in a cold climate is seen in the photograph above, which depicts condensation of interior vapor that has occurred at the gypsum sheathing behind non-breathable Grade B paper during a period of cold winter weather.
The Grade B vapor barrier seen in this photograph is installed at the cold-in-winter side of the wall’s insulation improperly, contrary to the requirements of IRC Section R318.1 that a “vapor retarder shall be installed on the warm-in-winter side of the insulation” except “in construction where moisture will not damage the materials” or “where the framed cavity is ventilated to allow moisture to escape.”
The authors of the IRC burden the building designer with the primary responsibility for understanding how the breathability of a specific building paper or wrap may impact the overall performance of the building envelope; however, during the course of residential mold or moisture damage litigation, the key question of who actually designed the building envelope sometimes can be difficult to answer. Is it the architect who produced a generic set of plans but did not specify any particular product, or is it the builder whose purchases at the lumberyard perhaps were based solely upon availability or price, not technical performance issues.
In any case, a good resource for residential architects and builders seeking to gain a better understanding of fundamental building envelope design issues is the free 88-page manual Durability by Design: A Guide for Residential Builders and Designers, published by HUD (available atwww.huduser.org/publications/destech/durdesign.html). W&C
Footnotes
Polyethylene and/or polypropylene
See definition of “approved” in Chapter 2, Section R202
2003 International Residential Code
ASTM D 4869, Standard Specification for Asphalt-Saturated Organic Felt Underlayment Used in Steep Slope Roofing, ASTM International, West Conshohocken, PA, 2005
ASTM D 226, Standard Specification for Asphalt-Saturated Organic Felt Used in Roofing and Waterproofing, ASTM International, West Conshohocken, PA, 2006
One perm is equal to one grain of water vapor per hour per square foot per inch of mercury vapor pressure difference
Report Abusive Comment