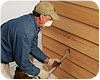
Current market conditions have created a perfect climate for insulation retrofits and the cold weather months are in full swing. Homeowners are staying put longer as homes are still lagging in resale value according to a recent report from the National Association of Realtors. As of July 2011, residential remodeling permits increased by 24 percent compared to the year before, rising to the highest level since 2004.
One popular home upgrade is making drill-and-fill insulation applications. Best-suited for enclosed spaces such as walls, the advantages of drill-and-fill insulation projects are clear; keeping aesthetics intact while ensuring a home is less drafty, more comfortable and more energy efficient. However, many contractors and insulation installers still debate the ideal loose-fill material for the project.
The two most popular materials choices for drill-and-fill applications are cellulose and loose-fill fiberglass. While each has its advantages, it’s important to carefully evaluate the performance characteristics of each material. Key characteristics worth considering include thermal and air resistance, ease of installation, cost and availability, settling, recycled content and indoor air quality.
THERMAL AND AIR RESISTANCE
The thermal resistance of insulation, the R value, is one important consideration. When looking solely at R values of the two products in dense pack, drill-and-fill applications, fiberglass can provide a higher R value with less material than cellulose.
Additionally, loose-fill fiberglass products can provide up to 30 percent better air resistance than cellulose when installed at recommended densities for drill-and-fill applications.
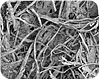
While the tools and techniques used for drill-and-fill applications remain somewhat consistent regardless of the product, the materials used to create each product affect its ease of installation.
Cellulose fibers, produced by grinding-up newspaper and other paper products and then adding fire retardant chemicals, vary significantly in size and durability depending on the paper stock (for example, newspaper, books or cardboard).
Compared to course-fiber cellulose, fiberglass fibers have a smaller and more consistent fiber diameter and nodule size making the installation process smoother and more consistent.
Because products such as fiberglass insulation are recommended to be installed at significantly lower densities than cellulose (one and a half pounds less per cubic foot), the product is installed with less air pressure reducing the possibility of hose clogging and wall damage.
Finally, loose-fill fiberglass can be installed through very small holes, such as brick veneer mortar joint, and can be installed in cavities with existing batt insulation to increase the R value and air resistance of the insulation in the cavity.
COST AND AVAILABILITY
As with any product, costs will vary depending on the exact product and brand. While insulation costs can differ on a per-square-foot basis, keep in mind that dense packing can influence the amount of material needed for the same space.
Dense packing-in which loose-fill insulation is blown under heavy pressure into an enclosed cavity-is required for optimally efficient wall retrofits. The recommended dense-pack density for cellulose is 3.7 pounds per cubic foot where, for fiberglass, dense packing requires 2.2 pounds per cubic foot. Be sure to factor this in when accounting for cost.

Settling is an important factor to consider when evaluating products for drill-and-fill applications because it directly impacts the products’ installed performance.
Cellulose is more prone to settling because of the weight of the fibers, the size difference of the fibers and the additional weight of any moisture absorbed by the fibers.
Loose-fill fiberglass products are less prone to settling. Fiberglass insulation does not settle in a cavity when it is installed at densities of 1.5 pounds per cubic foot or higher. That’s because the insulation fibers are flexible and are slightly compressed during installation. Once the air pressure is reduced, the fibers attempt to spring back to their original shape which results in the fibers suspending themselves in the cavity. This characteristic of the glass fibers is evident in the way the fibers expand when the bag of insulation is cut open.
RECYCLED CONTENT
Homeowners have been giving increased attention to recycling and recycled products as concerns about our environment have heightened.
About 80 percent of cellulose is from recycled newspapers, one of the largest components of residential waste, while the other 20 percent is made of fire retardant chemicals.
In its final form, some fiberglass insulation can be highly compressed when packaged, requiring less packaging and less space in transit, which reduces fuel demands.
According to the North American Insulation Manufacturers Association, fiberglass insulation is the largest secondary market for recycled glass containers. The recycled glass used in fiberglass insulation saves more than 27 million cubic feet of landfill space every year, or 2.2 billion pounds of recycled post-consumer glass.
INDOOR AIR QUALITY
The average person spends about 90 percent of his or her time indoors, often in an environment more polluted than outside air, which is why the U.S. Environmental Protection Agency considers indoor air quality one of its top environmental concerns. One indoor air concern involves formaldehyde levels in the home.
When evaluating loose-fill fiberglass, contractors should look for products that improve indoor air quality by reducing formaldehyde levels in the home.
Cellulose is generally considered to have little to no negative effect on indoor air quality, as it’s absent of volatile organic compounds, such as formaldehyde, however the dust from cellulose and ink from the newspaper print can cause concerns for some people.
In closing, the drill-and-fill installation practice can be a great service to offer as an insulation contractor to homeowners, given the energy savings and comfort improvement it can offer. Also, with the increased use of infrared cameras, it is significantly easier to look into walls and see the energy being lost in both the summer and the winter. New loose-fill fiberglass products are providing contractors with new options, options that will withstand the scrutiny of those same infrared cameras that help to sell the service in the first place.
Considerations for Installation
Avoid voids and gaps. Voids and gaps occur if the insulation isn’t installed to proper density specifications or if a cavity isn’t completely filled. Voids also occur if the installation holes are improperly located between the vertical framing studs or if there are too few fill holes.Always install according to the amount of insulation required to obtain a particular R value per square foot (or square meter) of space.
Wear a quality respirator, protective eyewear, and clothing such as goggles, gloves, long-sleeved shirts, and pants to minimize contact with the insulation.
Report Abusive Comment