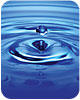
Water sustains all life on earth. But it is also nature’s universal solvent. Water causes more building enclosure failures than any other agent. Whether a failure results from excessive metal corrosion, or the spalling or displacement of masonry or concrete elements, water is often the prime catalyst. Without proper envelope detailing and an active maintenance program, building enclosures are at the mercy of the environment and the destructive force of water.
What makes water so destructive? On the atomic level, water is made up of two hydrogen atoms and one oxygen atom. The molecule itself is neutral, meaning it has no charge. However, a closer look at the molecular structure reveals that the two smaller hydrogen atoms bond to one side of the larger oxygen atom, creating a polarity effect, which allows water to dissolve nearly anything. This is just one of the many properties that makes water critical to the health and well-being of humans and our environment. When ingested, water dissolves and flushes out toxins in our bodies. However, it is this same property-the ability to dissolve almost anything-that degrades building materials.
Water can take on various states of matter such as vapor (steam or evaporation), liquid, and solid (ice). These varying states of matter have differing effects on building materials. The transition from one form to another, e.g., from liquid to solid and from liquid to vapor, is often the cause of the degradation.
The building enclosure failures that we will describe occur when water is introduced to the system because of faulty design detailing of the exterior enclosure, poor workmanship during construction, or negligent maintenance. We find the following typical water-related failures during our investigations: corrosion of metals, delamination, cracking, spalling, and displacement of stone and cementitious materials; erosion of sedimentary materials; and the wood decay and degradation of other organic material.
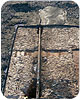
Photo 1: Water intrusion through built-up roof
system caused metal conduit to corrode.
Water is the prime catalyst of the corrosion of metals. One common form of corrosion, galvanic corrosion, results when two dissimilar metals are in contact and water is present and serving as an electrolyte. The electrolyte produces an electric charge, and the less noble metal will degrade and corrode. When corrosion is present, the material expands in volume, often disturbing adjacent materials. Photo 1 depicts a building envelope failure compounded by the corrosion of metal. Water intrusion through a defect in a built-up roof system caused a metal conduit located within the roof deck assembly to corrode and expand. The force of the expansion created a larger void in the roofing, allowing more water to enter the system. This condition, exacerbated by the expanding metal conduit, eventually dissolved the gypsum roof deck, providing a venue for the now-exposed steel roof framing and reinforcing bars to corrode.
Displacement of Stone and Cementitious Materials
Stone and cementitious building materials, such as concrete and brick are porous. They can absorb a significant amount of moisture, making them prone to the effects of freeze-thaw cycles in colder climates. When water is absorbed into these materials, it fills the pores of the material, much like a sponge. When the water freezes, it expands within the pores, creating tensile stresses in the structure of the material. Natural stone and cementitious materials have low tensile strength, and the internal stresses exerted within the material cause cracks, delamination, and eventually spalls of the surface layer (Photo 2).
Water expands equally in all directions. When trapped in confined spaces, such as joints between masonry materials, freezing water can exert powerful forces on surrounding materials, causing those materials to move in ways they were not intended or designed to move. Joints between coping stones on top of walls and parapets are susceptible to freeze-thaw damage. When mortar fails between adjacent stones, a path for water penetration is created. The forces exerted on the stones by the expanding ice can cause the stones to displace from their original positions (Photo 3). If this condition is not corrected through proper maintenance, the resulting area for water accumulation becomes larger as time passes, more space is available for more ice to form, and the cycle continues, until an unsafe condition develops.
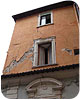
Photo 2: Stucco and masonry cracking and falling
from façade.
The effects of water’s cohesive properties are typically evident on older sandstone and brownstone elements. As water flows across building materials, especially those that are sedimentary, the surface of the material begins to erode, resulting in the loss of material cross-section. Generally, the dressed façade of the stone (like the patina on a metal surface) is microscopically washed away, leaving the raw, more porous inner layers of the material exposed to the weather. As the materials erode, they become more porous and absorb more water, further creating the potential for freeze-thaw damage and exponentially increasing the likelihood of structural failure.
DEGRADATION OF ORGANIC MATERIAL AND FIBROUS BATT INSULATION
Wood is also a porous material, with a longitudinal internal cellular structure. The natural condition of wood makes it a breeding ground for fungi. With elevated moisture levels, it provides a food source for the fungi, which feed on the interior cellular structure. This removal of material leaves a brittle matrix of chemical compounds found in the wood cells. Unfortunately, the structural compounds can become exhausted, which can lead to a condition commonly known as dry rot. In a constantly wet environment, wood performs well. When wood is exposed to wetting and drying cycles, it begins to expand and contract, non-uniformly, which can lead to the settlement of a structure. We commonly see this occur at wall sill plates atop foundation walls.
Similarly, when fiberglass batt insulation becomes moist, as a compounded result of many failures of the types previously mentioned, it loses its ability to resist heat transfer. The glass fibers that make up the core of batt insulation create air pockets within the insulation that resist heat flow. The more void air volume, the higher the R-value the batt will provide. Moisture in the voids reduces the amount of air in the insulation, thus reducing the amount of resistance to heat transfer.
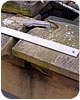
Photo 3: Displacement of roof parapet cap.
Generally speaking, an effective building enclosure serves as a barrier to the transfer of heat, air, vapor, and water. As this article only deals with the effects of water, the following are vulnerable areas where a designer must pay close attention to the detailing of the systems: window perimeters, transitions between varying materials, expansion joints, extents and joints in metal through-wall flashing, barrier wall systems, roof to rising wall conditions, and countless others.
We often find that designers and contractors use sealants as the only line of defense against water intrusion through the envelope systems. Sealants can fail immediately after application if not installed properly (e.g., if the substrate surface is not properly cleaned and primed) or not installed with the appropriate geometry to withstand the movement to which it will be subjected. Failures in sealants provide an avenue for air and moisture intrusion into the systems, which can lead to many of the issues noted previously.
TIPS FOR PROPER DETAILING
Without proper enclosure design and detailing, workmanlike construction, and a diligent maintenance program, buildings are susceptible to failure. The following tips help avoid common detailing errors that result in the degradation of the building enclosure:
Do not rely on sealant as the only line of defense against water and air infiltration. We recommend a sheet membrane to bridge the gap between materials or adjacent systems. A sealant joint and backer rod should be installed outboard of the membrane as a cosmetic seal.
Lap materials so that they shed water.
Apply a rain-screen approach to cladding: Clad the building with a material that meets your aesthetic intent and provide a robust backup waterproofing system that will drain accumulated moisture out of the system. Provide ventilation for the drainage cavity so that the materials that become wet from incidental moisture intrusion can dry out.
Provide a nominal slope to drain water off horizontal surfaces and projections, such as window sills, stone bands, metal flashing, roof edge coping, etc.
BUILDING MAINTENANCE
Proper maintenance is the key to the durability of any building enclosure. Depending on the type of enclosure system and the expected level of performance, the maintenance plan, frequency, and cost will vary.
We recommend that a comprehensive annual survey of the building envelope systems be performed. Review areas where there are sealants, transitions in façade materials, window sills, roof transitions, etc. With a yearly checklist of maintenance issues to repair damage from long-term, compounded water intrusion, the safety of the public and building occupants can be preserved from the effects of water.